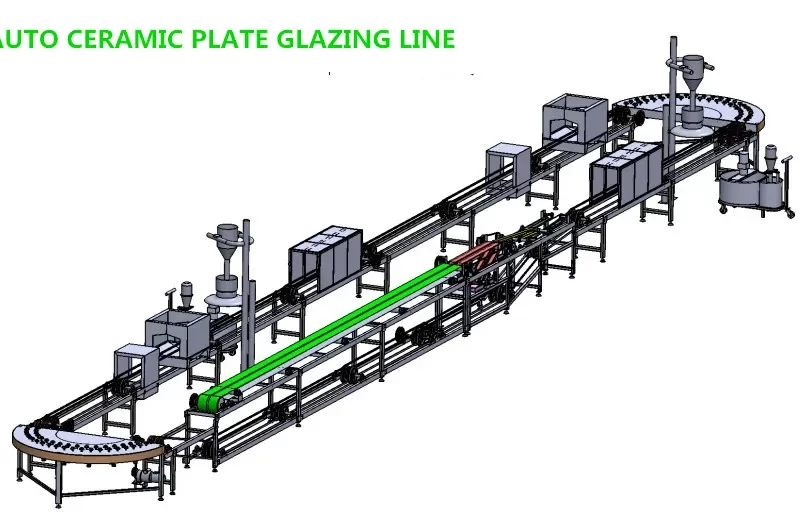
In der modernen Keramikindustrie ist die Verbesserung der Produktionseffizienz zum vorrangigen Ziel der Keramikhersteller geworden. Angesichts des zunehmenden Wettbewerbs auf dem Markt stehen die Keramikhersteller vor der Herausforderung, ihre Kapazitäten zu erhöhen und die Kosten zu senken, während sie gleichzeitig die Produktqualität sicherstellen müssen. Die Einführung von automatisierte Keramikmaschinen bietet eine wirksame Lösung für diese Herausforderungen.
Automatisierung in der Tonaufbereitung
Traditionell Tonaufbereitung wird häufig manuell betrieben, was ineffizient ist und die Gewährleistung von Gleichmäßigkeit und Qualität erschwert. Unsere automatisierten Anlagen zum Mischen, Sieben und Fördern von Ton garantieren eine stabile Tonqualität und eine effiziente Aufbereitung durch präzise Proportionen und hocheffiziente Siebmechanismen. In einem Fall reduzierte ein Hersteller von Keramikschalen, der diese Anlage einführte, die Zeit für die Tonaufbereitung um 30%, was die Effizienz der nachfolgenden Produktion verbesserte.
Innovative Automatisierung in der keramischen Formgebung
Die Keramikformung ist ein entscheidender Schritt im keramischen Herstellungsprozess, aber herkömmliche Methoden sind durch die Präzision und Geschwindigkeit manueller Vorgänge begrenzt. Unser Keramikformautomaten verwendet eine fortschrittliche Werkzeugtechnologie und ein PLC-Programmsteuerungssystem, um eine erhebliche Verbesserung der Gussgenauigkeit und -geschwindigkeit zu erreichen. Nach dem Einsatz dieser Ausrüstung konnte ein Partner seine Formeffizienz um 50% steigern und die Ausschussrate senken.
Optimierung des Trocknungsprozesses durch Automatisierung
Nachdem die Keramik-Trocknungsmaschine wurde mit Automatisierungstechnik aufgerüstet und kann eine intelligente Temperaturregelung und gleichmäßig verteilte Windgeschwindigkeit durchführen. Dies verkürzt nicht nur die Trocknungszeit, sondern verbessert auch die Konsistenz und Stabilität des Produkts. Es kann die Trocknungszeit um 20% reduzieren und die Produktqualifikationsrate erheblich verbessern.
Innovationen in der automatisierten Verglasung und Aufkleberanbringung
Einige Hersteller lassen die Glasur oder die Abziehbilder von Hand aufbringen, was jedoch die Produktionseffizienz und die Qualitätskonsistenz stark beeinträchtigt. Die automatische Keramik-Glasiermaschine Es genügt, den Embryo auf das Förderband oder einen Manipulator zu legen, und die Maschine kann die Glasurarbeiten automatisch ausführen. Die präzise mechanische Steuerung und die stabile Glasurzufuhr sorgen für eine gleichmäßige Glasur und die Genauigkeit der Abziehbilder.
Aufrüstung der Ofenfeuerung mit Automatisierung
Keramischer Brennofen Das Brennen ist der letzte Prozess der Keramikformung und das energieaufwendigste Glied. Konzentrieren Sie sich auf die Kombination von automatischen Temperaturregelungssystemen mit der Verbesserung der Ofenstruktur, um die effiziente Nutzung von Energie zu optimieren. Hersteller, die ihre Öfen aufgerüstet haben, konnten die Brennleistung um 25% steigern und den Energieverbrauch um 15% senken.
Umfassende Nutzenanalyse
Die Einführung des automatische Keramikmaschinen nicht nur die Produktionskosten gesenkt, sondern auch eine doppelte Verbesserung der Effizienz und der Produktqualität in jedem keramischen Produktionsprozess erreicht. Die Praxis vieler Partner hat bewiesen, dass die automatische Produktionslinie die Effizienz der Keramikherstellung erheblich verbessert.
Schlussfolgerung
Da sich die Keramikindustrie weiter entwickelt, werden automatisierte Keramikmaschinen ein wichtiger Trend zur Verbesserung der Fertigungseffizienz sein. Wir freuen uns darauf, dass mehr Keramikhersteller diese innovativen Technologien erforschen und anwenden und so gemeinsam die erfolgreiche Entwicklung der Keramikindustrie vorantreiben. Wir laden Sie ein, mehr zu erfahren Lösungen für die Herstellung von Keramiken mit uns eine glänzende Zukunft für die Keramikherstellung zu schaffen!